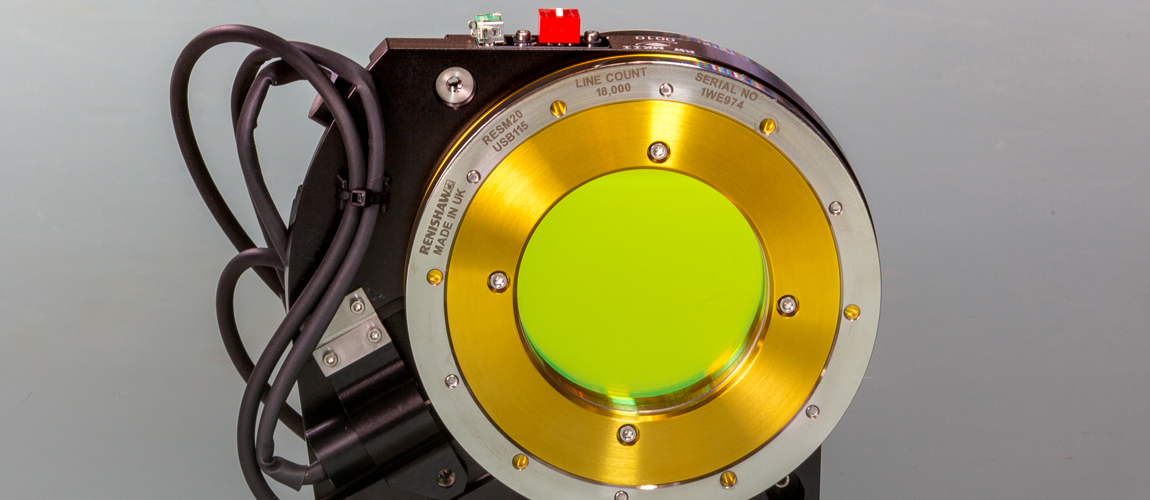
Innovations
New Applications with Carbon
Our main field of work is supporting space missions, delivering light-weight carbon parts, such as CFRP beams or CFRP substrates for solar panels. At CST we are open to new challenges and projects outside our comfort zone – this characteristic empowers us to design products and processes for various industries and applications.
For Space and Industry
Making use of carbon properties like ultra light-weight and high stiffness, we invented a zero gravity testing device, called ZeroG robot, for realistic space product testing. But we also gained ground in the production and testing of semiconductors with our compact Rotating Wedge for laser beam steering, making use of a Risley prism.
Rotating Wedge
Compact & robust solution for laser beam steering
At CarboSpaceTech, we developed a Rotating Wedge for applications that require laser beams to be aimed at distant targets. This compact, robust and economical device for beam steering was designed for Hensoldt for use in semiconductor industry.
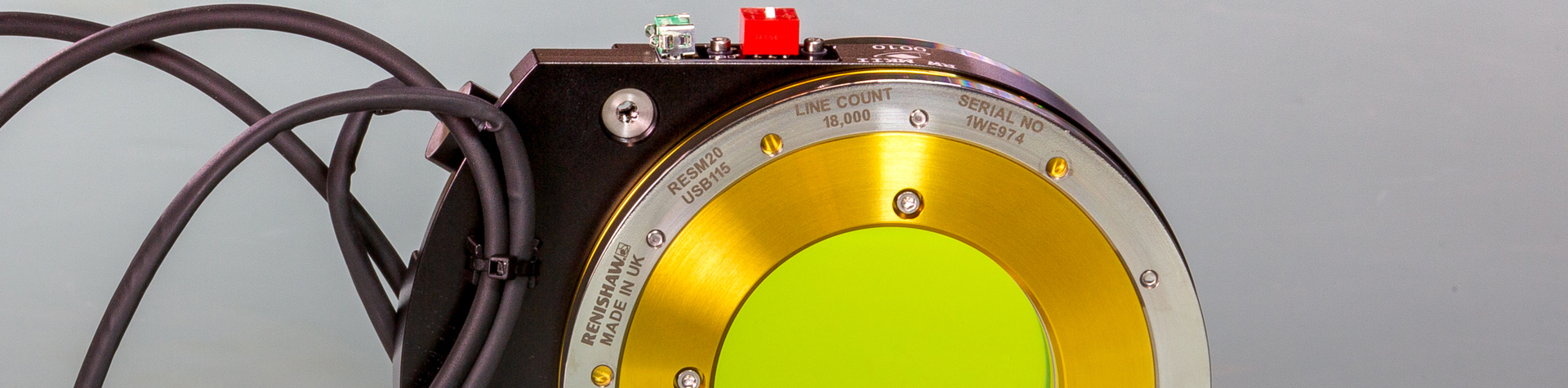
Risley prism
The CST Rotating Wedge is based on a Risley prism. The beam deflection is only dependent of the rotation of prisms around the optical axes which is measured directly and highly precise. The system is therefore resistant towards positioning in the beam path as well as environmental conditions such as temperature or vibration.
Key features of Rotating Wedge
- Compact, space saving solution
- Robust design
- Enhanced lifetime
- High speed
- High resolution encoding
- Back lash free
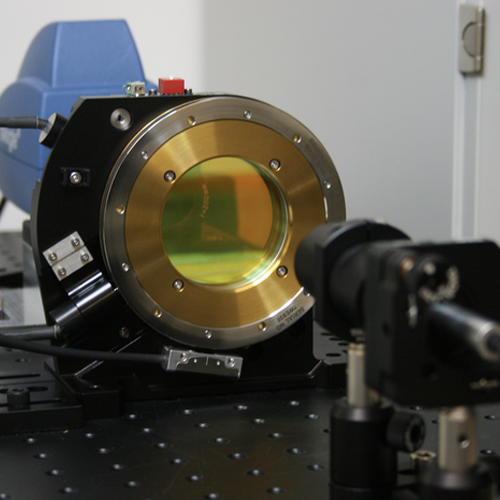
Rotating Wedge technical information
Risley prisms work in pairs. The two prisms are oriented in a way so that they deflect light in the same direction and therefore work as a single prism. Thus, offering the advantage of doubling the angle.
Example 1: If each prism is rotated about the optical axis by the same angle but in opposite directions, the beam is deviated by a small amount but stays close to the level defined by the optical axis and the refracted beam.
Example 2: If the prisms are rotated by 90°, they act parallel with no angular deviation.
The beam deflection only depends of the prisms angles and is insensitive towards external influences such as vibration or temperature. An in-house designed calibration technique provides very high absolute precision of the beam deflection.
The system is optimized for a long lifetime (downtime and propagation).
With the BLDC motor, very high speed can be reached.
For our Rotating Wedge we use an encoder with high resolution at nm range.
We are using a back lash free drive with excellent controllability.
Zero gravity testing
Gravity is critical for testing space equipment in a realistic environment. By using this revolutionary simulation tool, CarboSpaceTech aims to avoid gravity impact during testing. Reach the next level of zero gravity testing for space equipment with the ZeroG robotic arm.
Gravity-free space product testing with CFRP-based ZeroG robot.
Increase mission success, save time and money with realistic testing of space applications
ZeroG principle
ZeroG uses different methods for compensating in the XY plane (horizontal) and Z axis (vertical). The basic principle for XY is to suspend the test object on a rope, and making sure that this rope is as vertical as possible during the test. A sensor measures this rope angle and robot manipulator, driven by a “closed loop” control system, ensures minimal deviation from true vertical. Prior to testing, a calibration is done by suspending a mass that is not affected by external forces. Using this mass as plumb line ZeroG can automatically find true vertical for multiple points in the working area. In the Z-Axis (vertical) ZeroG ensures constant force by measuring the force in the rope and actively controlling the rope length using a high-speed winch. Therefore, ZeroG is able to eliminate the impact of gravity by keeping the force in the wire equal to the mass of the test object multiplied by G and minimizing the rope angle.
Key features of ZeroG robot
- Realistic test environment
- Increase mission success
- Save time and money
- Space-grade CFRP construction
- Wall mounted robot manipulator
- Floor mounted Z-servo
- Powerful computer
- Safety perimeter fence
- Implementation & documentation
- Analysis available
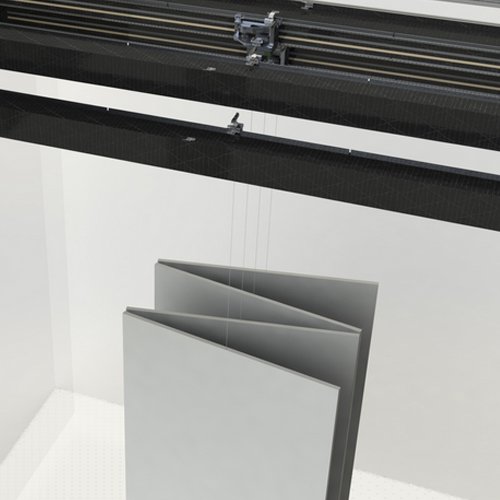
Multi-hinge solar
array testing with ZeroG
Different payloads and satellite specifications demand a variety of solar array surfaces. A larger surface can only be achieved by the use of multi-hinge solar arrays that connect several solar panels. CarboSpaceTech’s current development utilizes a ZeroG robot with multiple, independent manipulators – one for each of the connected solar panels.
Solar array deployment
mechanism for OneWeb
SZero gravity testing of controlled boom deployment is essential for the OneWeb Satellites mega constellation mission’s success. Our parent company, SpaceTech, is delivering key components for OneWeb satellites. CarboSpaceTech is responsible for the manufacture and testing of the CFRP booms for the OneWeb deployment mechanisms.
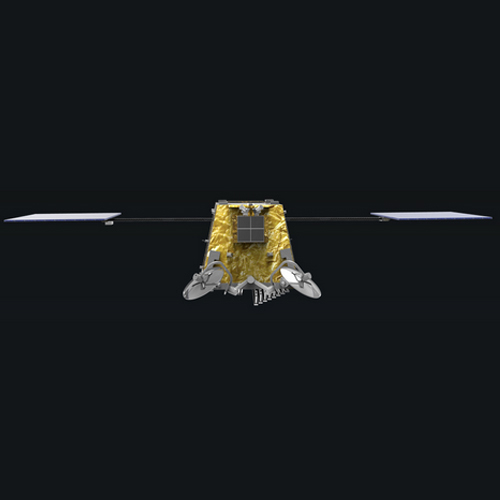
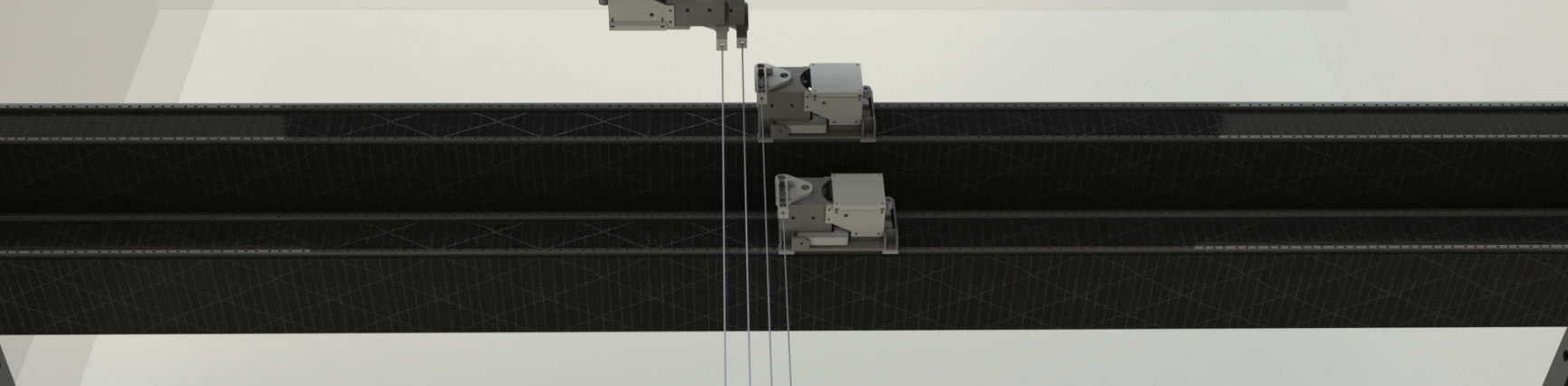
Customized
zero gravity
testing devices
At CarboSpaceTech, we pride ourselves in being quick to develop and deliver new systems tailored to our customer’s needs. We are always happy to discuss the requirements of your next level zero gravity testing device!
ZeroG testing of
multi-hinge
deployment mechanisms
The demand for of multi-deployment solar arrays for satellite power supply is steadily growing. Only with CarboSpaceTech’s zero gravity testing in a lab you can assure that these special mechanisms will function flawlessly later on in space. The new version of the ZeroG robot is able to test such multi-hinged arrays.
ZeroG robot technical information
- Resolution < 1‘‘ (0,0004°)
- Working area ± 1°
- Sampling rate up to 2 kHz
- Integrated CAN master
- 4 independent portals, each with 2 degrees of freedom. 3 x Elmo Gold Twitter for each portal: 2 x for traverse (x-axis), 1 x for sled (y-axis). All controllers are directly attached to the drives.
- Carbon fiber traverse
- Linear motors for both sides of the two portals. Both portals moving on same magnetic track.
- Friction wheel drive for y-axis
- Working load: 100 kg (only vertical load)
- Work space: 5400 mm x 2800 mm
- Maximum speed-up: 2 g
- Maximum speed: 2 m/s
- Band width of control cycle speed: 60Hz
- Collision avoidance between traverses with CAN-Bus
- High speed transition of raw data by Wifi
- Control cycle 600 Hz (currently regulated by CAN-Bus)